UPDATE ON LOGISITICS SITUATION
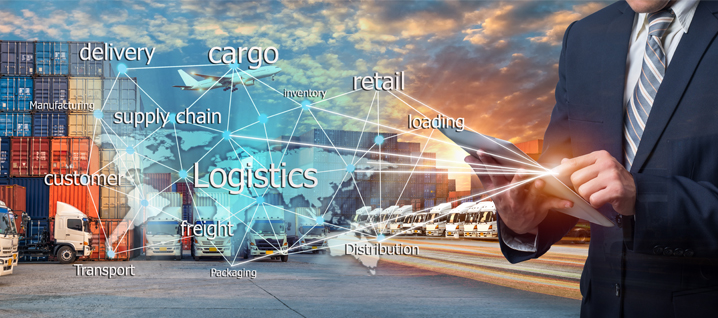
I wanted to give you a quick overview of what’s going on in our industry, with regards to product availability, backorders, ‘out of stock’ notices, so that you have a better understanding of the challenges we are facing, and to help you plan around these new timelines.
While the US has felt the pain a little quicker than here in Canada we are definitely feeling it here now.
CURRENT SITUATION WITH
GLOBAL SUPPLY CHAIN
NEW CONSTRUCTION
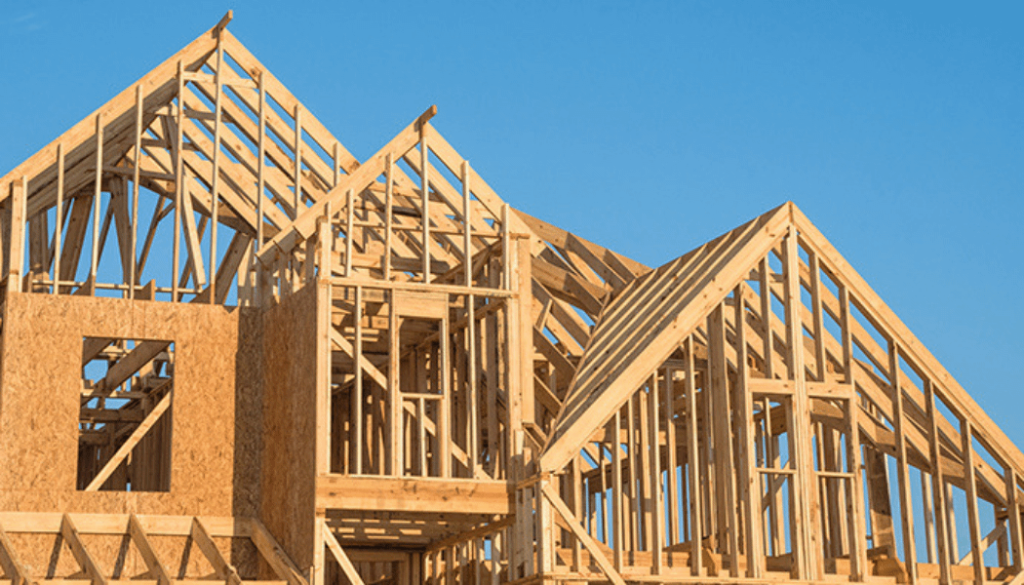
The surge in demand for construction and everything ‘home’ products went way beyond what anyone could have expected. This put an enormous amount of pressure on global suppliers, what with COVID shutting down factories, then, once re-opened, adhering to social distancing measures which in turn slowed down production, not to mention second waves that came and lingered and now possibly a third wave on the horizon, as is being experienced in Italy. We’ll talk LUMBER further on.
The amount of imports far outweighed what our exports were, and are, resulting in not enough shipping containers being returned for foreign ports, which in turn is causing a shortage of shipping containers to fill North American orders. There is little to no profit for carriers to return these empty shipping containers to their original locations.
SHIPPING CONTAINER SHORTAGES
Steel tariffs increased the cost of manufacturing said containers on our own soil. Looking to foreign manufacturers to make these containers resulted in excess demand with low output capacity, and not enough profit in it for them to get excited about making containers. It also caused a lot of companies to frontload their orders just to get product to North American shores before prices went up.
The demand for containers to ‘get products to shore at any cost’ started bidding wars between companies which in turn has increased the cost of a container by 175% to West Coast terminals and 75% to East Coast terminals.
Example 1: shipping container rate from Shanghai to West Coast went from $1600.00 to over $3600.00 per 40’ container.
Example 2: shipping container rate from Shanghai to East Coast went from $3100.00 to over $4600.00 per 40′ container.
Most of our suppliers resisted passing on these increase to us, and you the consumer, during 2020 as this was seen as a temporary event. They also didn’t want to further burden small and medium sized business with extra costs in order to help them sustain or recover from their financial losses.
Well, the demand is not showing any signs of easing up, and all of our manufacturers and suppliers can no longer continue to absorb the increase and are now passing this on to you the consumer. You will see higher prices in your ‘cart’ everywhere.
DISTRIBUTION TERMINALS
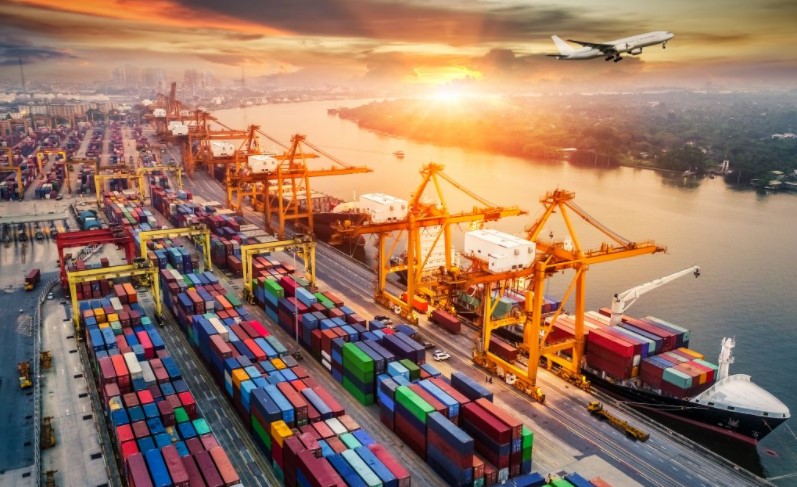
When the looming price increases started back in the fall, the container scarcity and continued surge in demand a lot of large retailers front loaded their orders just to get stuff ‘out the door’ before the price increase happened. This created a bottleneck at all North American terminals. COVID 19 impacted and reduced the amount of workers at these terminals. Throw in a couple of strikes at these ports, severe weather events, one fire, and you have a perfect storm for ongoing delays.
It normally takes 3 days, with a group of 6 teams, to offload a container ship as they work 3 shifts per ship per day. At the height of the pandemic they were down to 1 team and 1 shift per ship per day.
Ships are idling at sea waiting anywhere from 4-7 days before being called in to dock. This means that only 32% of all vessels are running on time, although this has improved slightly. Not to mention a ship sinking and losing it’s 3000 container load to the bottom of the sea earlier this year.
DISTRIBUTION CHANNELS
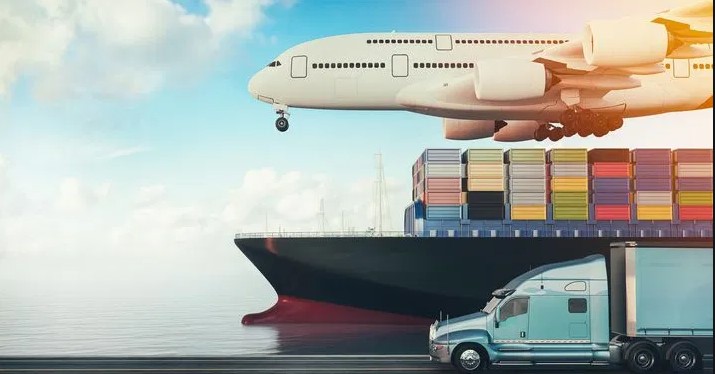
If you consider the surge for shipping containers, consider also the trickle down effect of getting the product off the docks and to your location. There are delays in getting stuff off the terminal tarmac and into the trucks or rail cars. Trucking is (or was) cheaper than rail…but when you ‘really gotta get it there’, rail car is faster and more efficient than trucking. This then started bidding wars for rail cars. Rail carriers also increased premiums by up to 20 and 30% depending on how far inland the train has to go. Then add in the trucking to get from the rail yard to the distribution centre. There are more trucks than rail cars in the logistics network.
TRUCKING
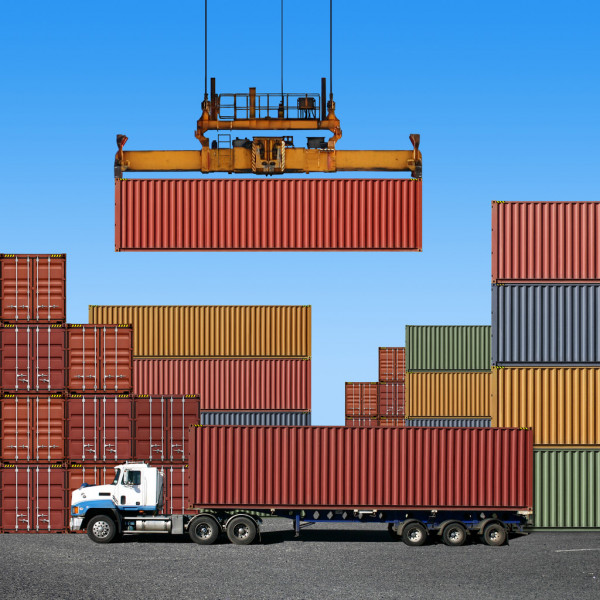
The trucking industry is reacting to all of this too. With excess demand and low capacity comes more product damage. There are driver shortages, deficient infrastructure, congestion across supply chain, outdated technology that hamper efficient moving of goods and products. Throw in the new carbon tax in Canada and fuel prices are playing into the price increases.
PASSENGER AIRCRAFT
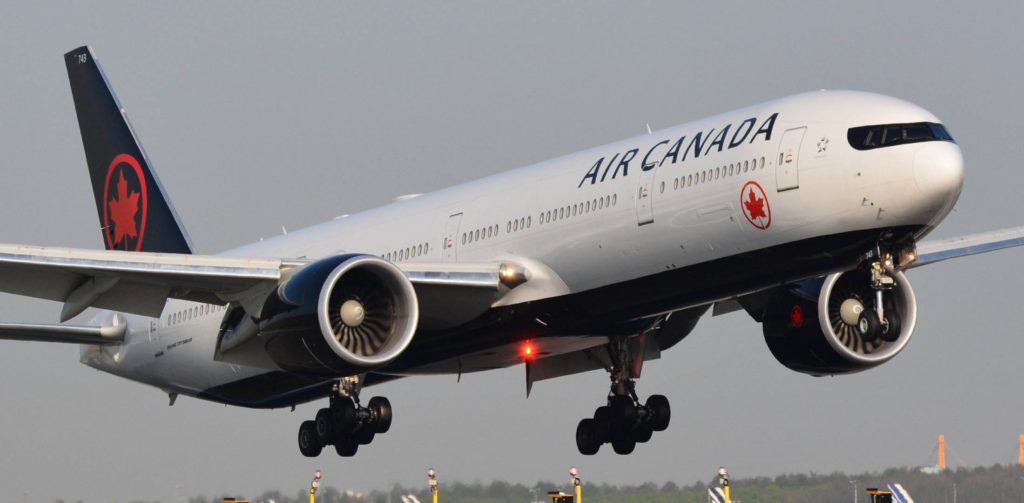
Passenger aircraft carry 54% or global cargo. With non-essential air travel restricted this reduced capacity as well. On the bright side we have a capacity to deliver vaccines.
The continued disruption of logistics is forecasted to continue through to mid-end of Q2, and that’s if the new COVID variants respond to existing vaccines, otherwise I predict that this will continue well into Q3 or Q4 until vaccination takes a giant leap forward here in Canada.
I’m pleased to share that most of my core suppliers and manufacturers are Canadian. That said some of the components they use in their manufacturing are not. As of today things are still progressing and processing well, other than the sheer volume of orders has extended lead times for manufacturing and product delivery.
UPHOLSTERY SECTOR
Besides the global supply chain issue, there is also a domestic issue with chemicals and foam used in upholstery manufacturing. Their problems started in Q2 of 2020 and kept compounding well into Q4 2020. The latest severe weather event that happened in Texas has again crippled this sector. In February the chemical and foam manufacturers declared a force majeure as their plants again closed down to recover from the damage the storm caused.
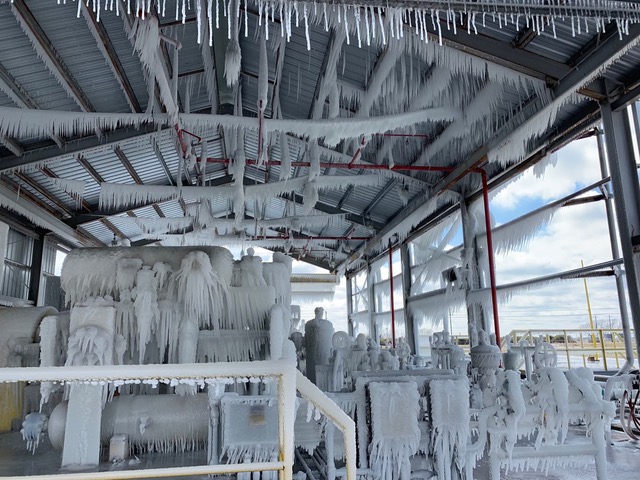
As they are slowly re-opening, this has forced them to institute allocation maximums for large and medium upholstery manufacturers. They are also still working through the backlog of orders from COVID, rising demand for new orders and no product, or reduced output of essential material to manufacture with. So that sofa or mattress delivery you were expecting in April or May is most likely being pushed out until June or July – maybe longer. If you have ordered any upholstery from the large chain or big box stores you will most likely receive a notice of delay. Unless your order was completed and in a warehouse waiting to be picked up.
I am happy to report that my custom upholsterer right here in Ontario confirms their foam supply is unaffected as they deal with a smaller and closer supply chains – who are still ok at this time. Current production lead times are steady at 10-11 weeks.
This is the best endorsement to ‘BUY LOCAL’ that I can think of.
LUMBER PRICES
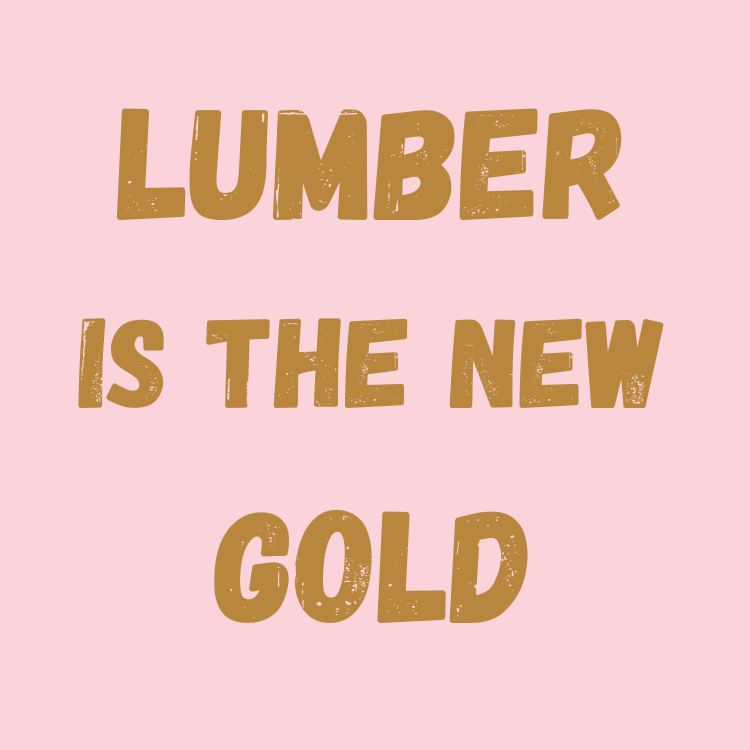
Lumber prices see no let up in their upward trajectory and are predicted to continue to rise through to Q3 2021.
While the pandemic would seem to have been the main cause of this issue in reality it was compounded initially by the Pine Beetle infecting large swaths of forests in parts of BC. Additional clear cutting measures were required to stop the spread of the infestation. Then, COVID hit shutting down saw mills and production literally grinding to a halt, a slow reopening and recovery, and a surge in demand.
Weather events around North America increased demand for lumber exports etc etc…you get the point by now. So hold on to those 2×6’s they’re worth their weight in gold!
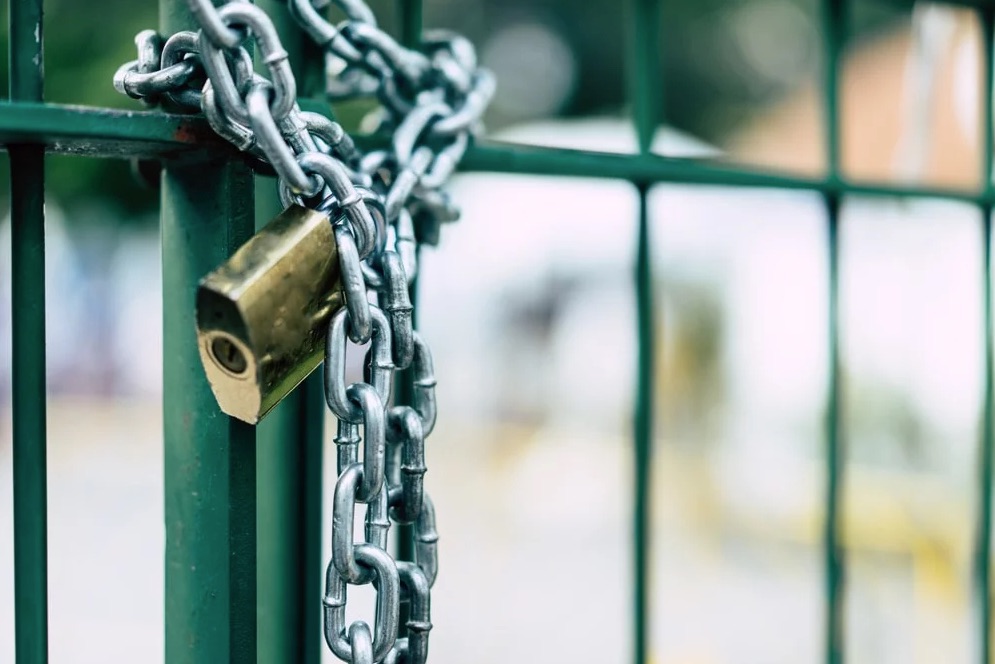
You might want to lock up your stockpile on your job site since theft of construction materials is also on the rise.
NEW CONSTRUCTION AND REMODELS
If you are planning a project this year make sure you have everyone lined up and committed to your project. There are not enough contractors and trades to keep up with the demand, put that together with projects, still ongoing from late last year, not yet completed because of product delays and labour shortage, and everyone is scrambling. This is pushing out new projects potentially even further than planned.
If you can buy and store any materials (construction and other), or at least anything that does not require a warranty registration, do that now so you can secure current pricing and stock. This will go a long way to keeping your project rolling along once started. You don’t want to get caught off guard by backorders or worse yet ‘out of stock’ notices.
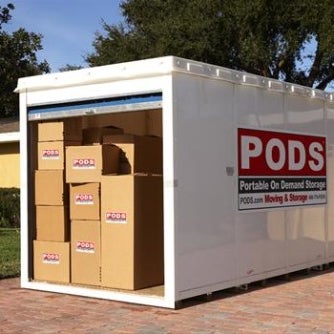
Appliances are another big issue these days so you need to get on it.
While suppliers and retailers can give you a ‘delivery’ date they are also at the mercy of the manufacturers and the supply chain. That date can change in an instant, and I have seen deliveries pushed back at least 4 times since last July.
Please be aware of this during your planning and preparations and make contingency plans for the ‘inevitable’ that is playing out more and more these days.
On a final note PLEASE BE KIND TO YOUR TEAM. They are doing what they can to provide you with the service, updates and timelines that they can for your project, given what we are all working with. We want nothing more than to have you living in, and enjoying, your new space and ease all of this stress away.
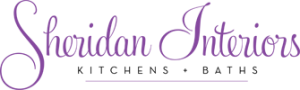
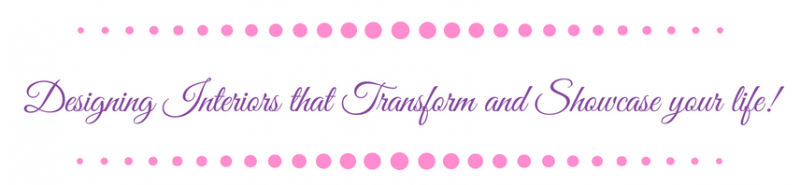